Warning
You are reading the documentation for an older Pickit release (3.3). Documentation for the latest release (3.5) can be found here.
What makes a good tool for bin picking?
In applications like bin picking, parts are randomly oriented inside the bin, and the robot tool must avoid collisions with the bin or its contents during the picking motion. This article focuses on robot tool best practices for such applications. Other applications, like depalletizing, have more lax constraints in these respects, and don’t necessarily need to incoroporate the recommendations presented here.
Tip
We highly recommend to select the robot tool for your application together with the vision system. We often see applications in the field that first finalize the hardware side of the application, including the robot tool, and then start looking for vision solutions. This ultimately leads to suboptimal tool choices and application performance.
You can in fact model robot tool candidates in Pickit to have a preliminary idea of how well they would perform, and benchmark them against each other before any tool hardware is built!
Gripper technology
There are many gripper technologies and application constraints that already limit the set of possibilities. For instance:
Magnets are only an option for magnetic parts, and some applications don’t allow parts to be magnetized.
Suction grippers are not amenable to some surface shapes, materials, and part weights. Ambient dust might also prevent their usage.
From the point of view of bin picking, take into consideration how parts can be presented in the bin, and select a gripper that maximizes the likelihood of reachable and successful picks.
The two most common categories of grippers are fingered grippers, which operate on the principle of clamping a part; and suction/magnets, which operate on the principle of attaching to the surface of the part. Below are examples where one should be clearly favored.
This ring-like part allows to be clamped by a gripper, both internally (shown) and externally (not shown). Conversely, the upward-facing surfaces are very small, which make it a poor choice for a suction or magnetic gripper.
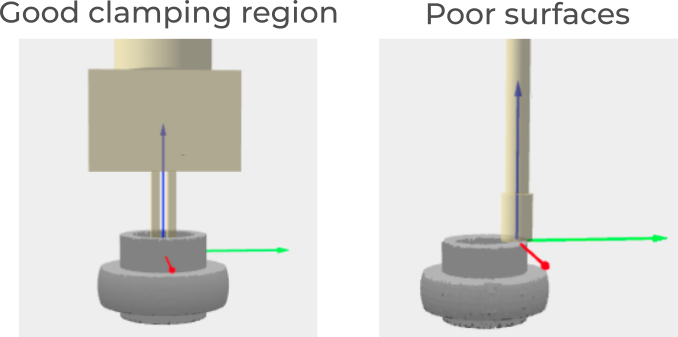
These parts are closely stacked together, such that there is no space left for a clamping device like a gripper to go in. However, the top surfaces are exposed for a suction or magnet gripper.
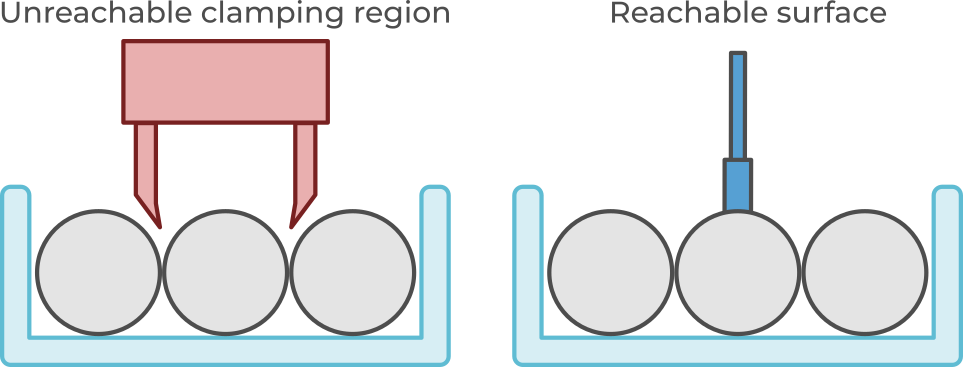
Slender tools
For bin picking applications, it’s recommended to use tools where the part that enters the bin has the smallest possible footprint. Bulky elements can be located near the robot flange, and connect to the tool tip by means of a slender element. If possible, it’s preferred that the robot flange doesn’t enter the bin at all during the picking motion.
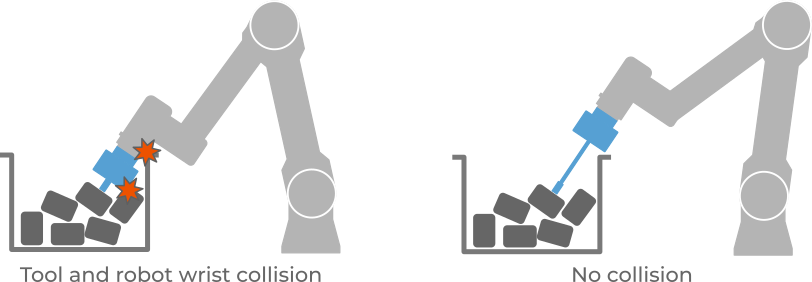
There are practical limits to how long a tool can be, such as mechanical stability, allowed robot payload, and robot reachability constraints. This is especially so when picking from deep bins.
Flexible pick orientation
Apart from slender designs, we additionally recommend tools that can tolerate some variation with respect to the nominal pick orientation without compromising pick success. Pickit tool models represent this as flexible pick orientation, and leveraging it produces more pickable parts, increases the likelihood of parts being reachable, and produces faster robot motions (shorter cycle times).
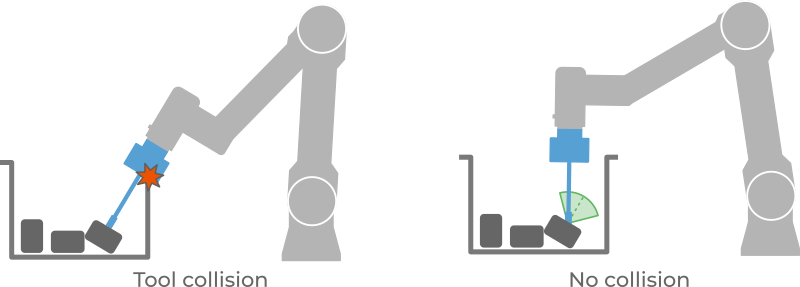
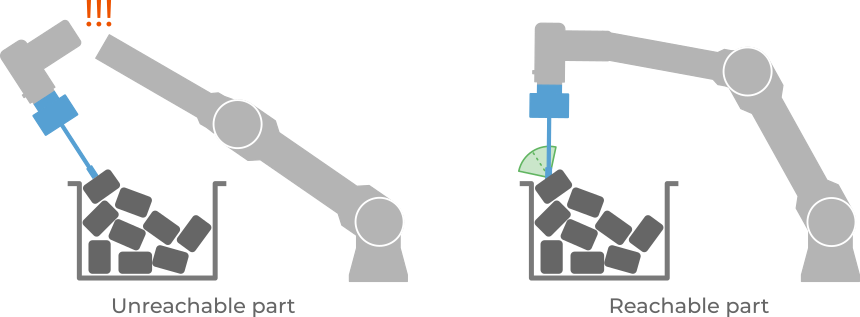
Note
Pickit offers application-specific gripper solutions that leverage this principle, and integrate seamlessly into the product. Learn more here.
A note on slanted tools
Slanted tools are sometimes used in practice, where a fixed tilt angle is built into the structure of the gripper. For example, the suction element or the gripper fingers are at an angle with respect to the main tool body.
This is a mechanically simple solution that increases the possible picks from one to two. However, a fixed slant angle is not equivalent to flexible pick orientation in terms of the possible picks it enables.
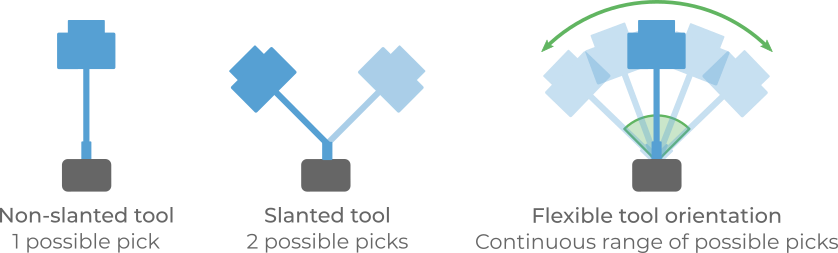
For example, consider a gripper with a fixed slant angle of 30° at the tip (below left and center), and compare it with a tool that can freely tilt between 0° and 30° (below right). Having a continuous tilt interval allows much more options from which to pick the part in the constrained scenario below.
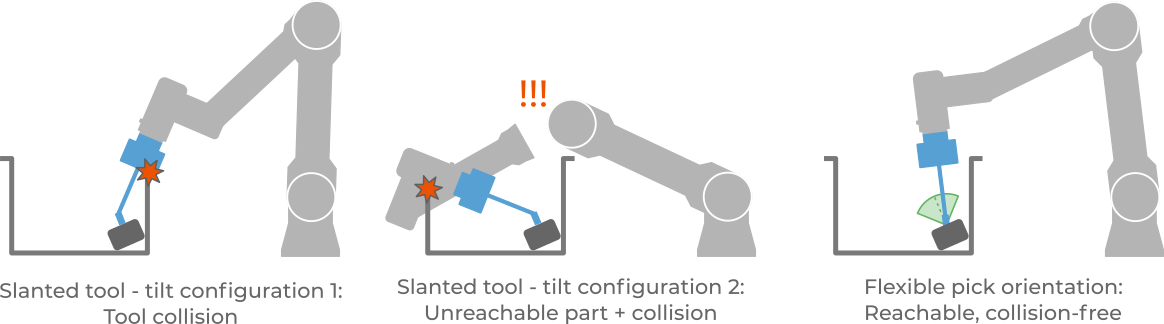
Compliance in the approach direction
It is often desirable for tools to have a compliant element along the pick approach direction, typical examples being suction cup bellows or springs. This element compresses to a certain extent when picking, and after retreating it goes back to its original uncompressed state.
Having such compliance helps to produce a firmer grasp, absorbs picking errors in the approach direction, and can help to prevent robot stops when unforeseen tool collisions take place.
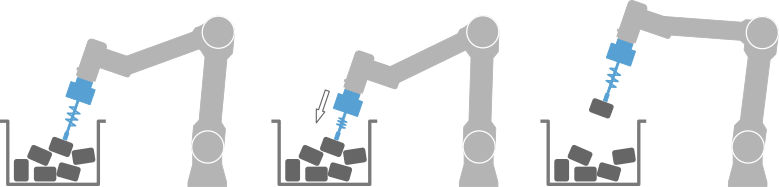
Refer to the article on TCP accuracy for guidelines on how to take this compliance into account when defining the robot TCP.
Tool configuration at the pick point
Tool design and pick point selection are two aspects that when considered together increase the likelihood of finding pickable parts and performing successful picks. The following recommendations exemplify such combinations:
Prefer internal grasps. They are less likely to result in collision and are self-centering, increasing pick accuracy without any additional step.
Use a tool configuration that tolerates positioning errors when approaching the pick. Using narrow and closed fingers in the below example makes the pick more robust to errors in the radial direction.
Pick points that are more tolerant to pick errors can be preferred by means of pick point priority.
Use a tool configuration that prevents certain collision modes typical in your application.
To pick the parts below when they are flush with the bin, a good practice would be to use eccentric fingers and allowing 180° flips for the tool Z rotation.
Pickit tool model
When modeling your robot tool in Pickit, make sure to follow these recommendations for correct and efficient collision prevention.