Robot integrations
Pickit integrates seamlessly with the major industrial and collaborative robot brands by means of Pickit robot integrations.
A Pickit robot integration is installed in your robot controller, and allows the robot to communicate using TCP over Ethernet with the Pickit processor (green cable in the figure below), which is where the Pickit software runs. You can then write a robot program in the robot’s native language that sends requests to Pickit (such as triggering object detection), and get results back (such as the detected object locations). All together, the commands exposed by the integration are the Pickit interface.
Robot integrations include ready-to-use programs that can be used directly for testing your application, or as a starting point for more complex applications.
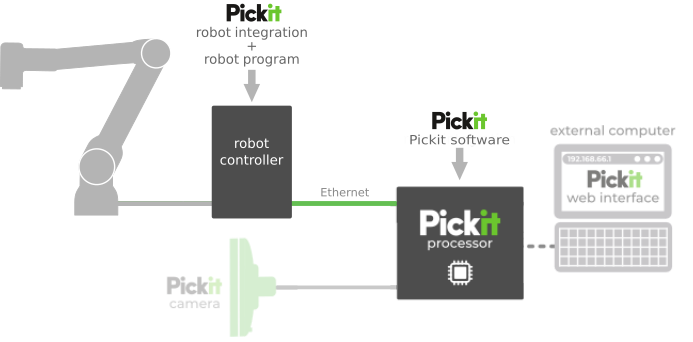
Robot Automation Scenarios
3D vision can be used to solve different types of applications, such as bin picking, depalletizing, or part location, which we call Automation scenarios. For each scenario, we have identified a number of best practices that the make robot program run efficiently and robustly.
The articles on automation scenario programs provide best-practice robot programs for a number of common applications, with detailed explanations. The idea is to minimize the time spent programming the robot by leveraging the provided application logic, and only performing minor modifications specific to your particular application.
Pickit interface
The Application Programming Interface (API) layer is what the robot programmer interacts with. This article can be used as a complete list of possible interactions between Pickit and the robot. Refer to socket communication instead to learn about the lower level socket interface.
Robot brands
In this section you can find the robot brands already supported by Pickit with a ready-to-use robot integration.