Warning
You are reading the documentation for an older Pickit release (3.0). Documentation for the latest release (3.5) can be found here.
Tool models and flexible pick orientation
In practice, many tools can tolerate some variation with respect to the nominal pick orientation without compromising pick success. Taking advantage of this can increase the likelihood that a pick point is pickable by the robot. This variation is typically due to:
Robot tool compliance, such as a passive hinge (below left), or flexible suction cup bellows (below center).
Application-specific constraints, like the clearance between the tool fingers and the object at the pick point (below right).
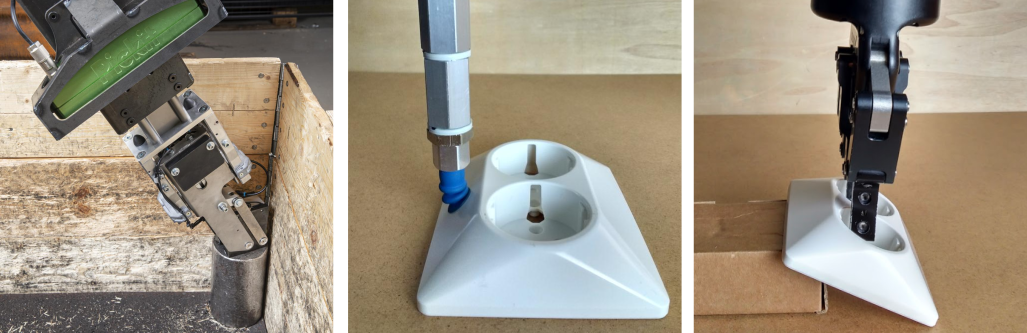
This article describes the features provided by Pickit to model such flexible pick orientation.
Tip
Apart from the flexible pick orientation of the robot tool model, multiple pick points and pick point symmetry axes are other strategies for increasing the likelihood of an object being pickable.
Flexible pick orientations, in combination with the preferred pick point orientation can be used to favor picks that are easier and faster to reach by the robot (e.g. less wrist motion, lower occurrence of unreachable points).
Flexible orientation at the pick point
Most tool models allow setting the optional Flexible pick orientation, which specifies the orientation flexibility allowed at the pick point.
Pickit allows the pick orientation to tilt around the X and/or Y axes, as well as to rotate around the tool Z-axis (below left). Flexibility around each axis is represented as a circular sector as wide as the specified interval size (below right). It can be visualized in the robot tool and pick point views.
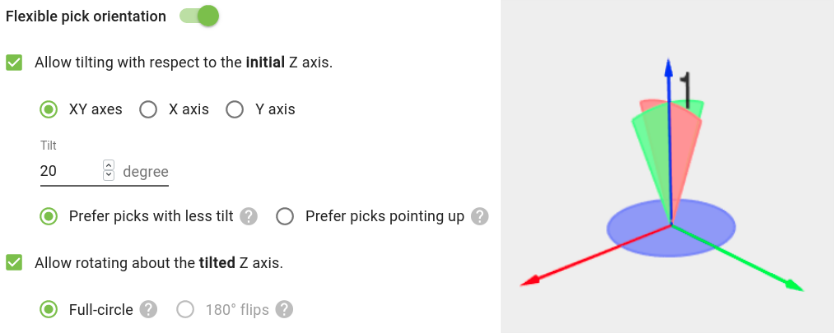
Tool tilt
Allowing a tool to tilt is associated with the following advantages:
More pickable objects, by avoiding robot tool collisions.
Reduce the required robot workspace, as pick points are more likely to be reachable by the robot.
Faster robot motions, which can translate into shorter cycle times.
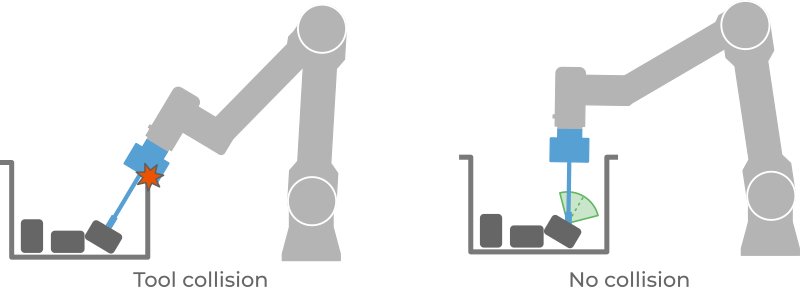
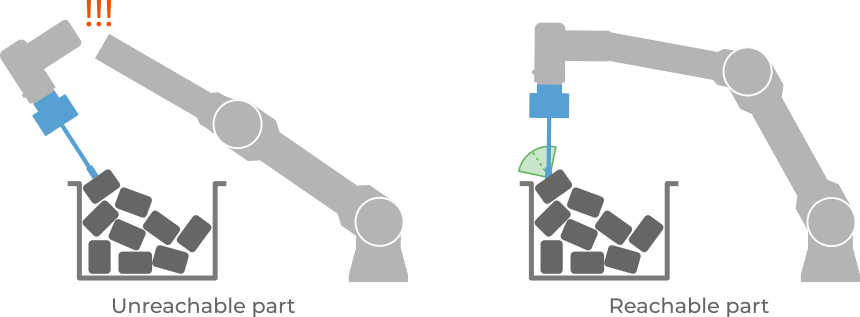
Tool tilt has three modalities, depending on the directions where tilt is allowed:
Tilt in XY: The tool can pick the part regardless of the tilt direction, up to a certain angle. An example would be a single suction cup (below left).
Tilt in X or Y: The tool can pick the part in the presence of tilt along a single direction, up to a certain angle. An example would be a two-finger gripper picking with clearance between fingers and object (below center).
No tilt: The tool does not tolerate any tilt. An example would be an asymmetric tool without any compliance (below right).
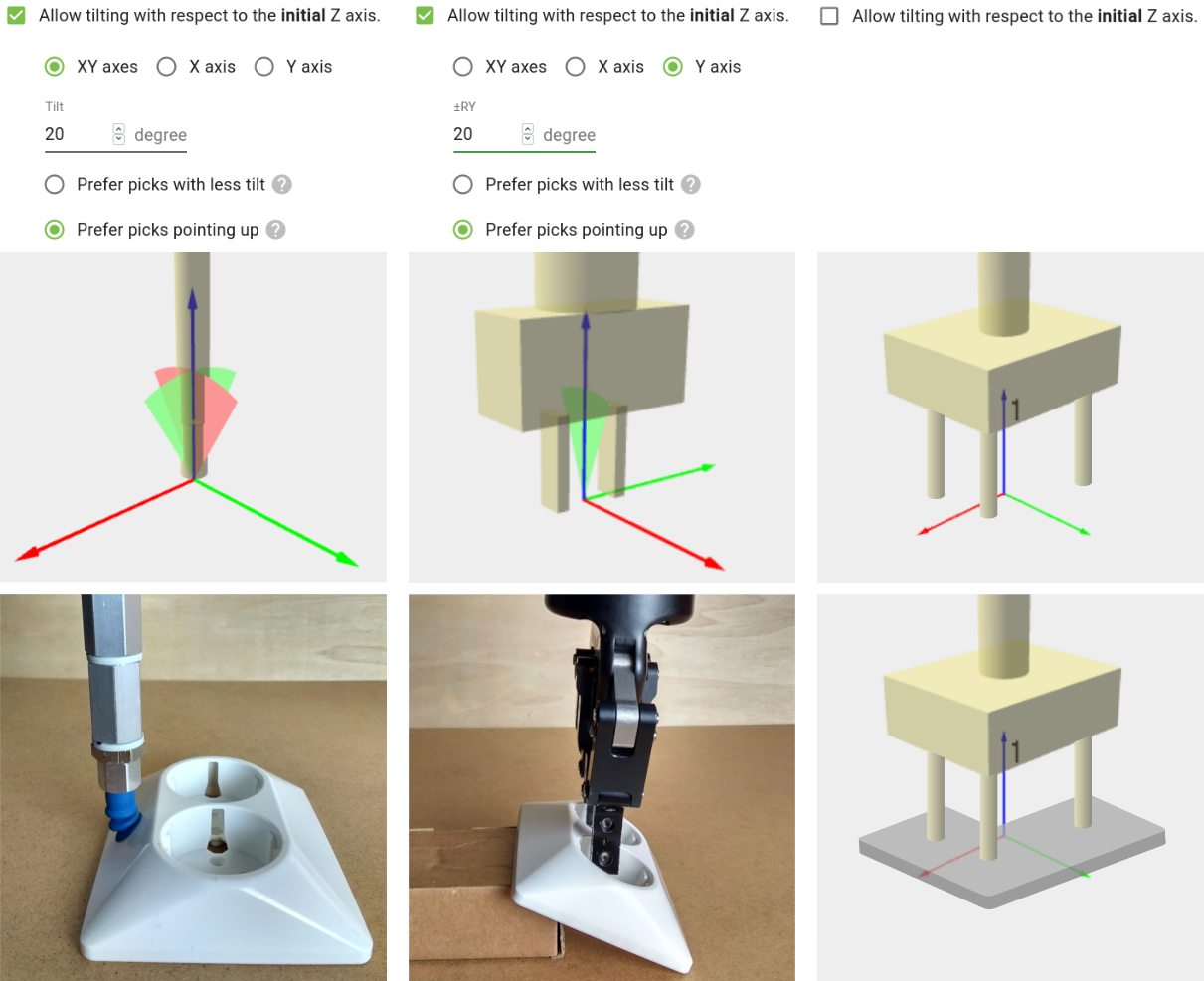
When tilting, it’s possible to instruct Pickit how much we want the tool to use this flexibility:
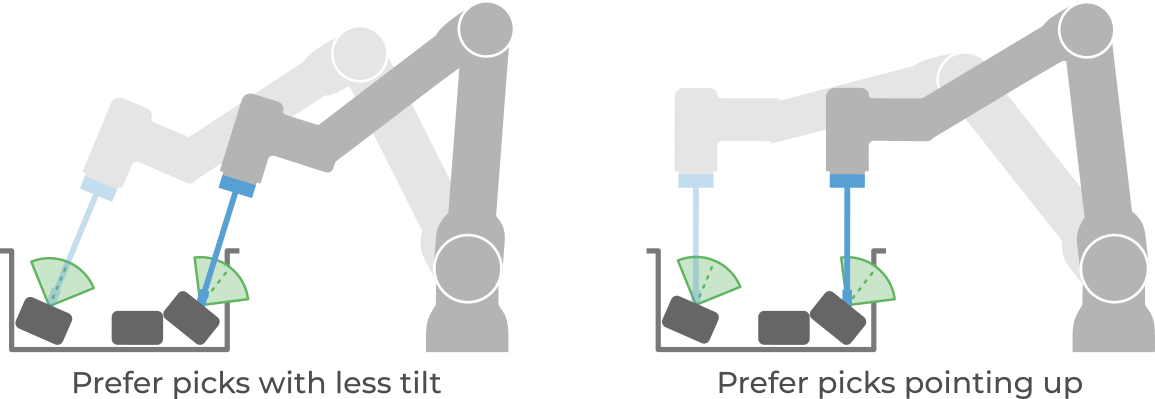
When Prefer picks with less tilt is selected, the tilting flexibility will only be used to make a point pickable, such as to avoid a collision between the robot tool and the bin or other objects (below, right pick). If apart from tilting, the tool additionally allows rotating about the Z-axis, this rotation will be used to align as close as possible to the preferred pick orientation. This is the default setting, and is recommended whenever tilting the tool decreases the likelihood of pick success. For instance, some suction cups might have more difficulty establishing vacuum when highly tilted.
On the other hand, when Prefer picks pointing up is selected, the tilting flexibility will be used to align as much as possible with the preferred pick orientation, which points up. Prefer this setting when you want to minimize tilting of the robot flange.
The below image shows the difference between the two alternatives for a gripper allowed to tilt 30°.
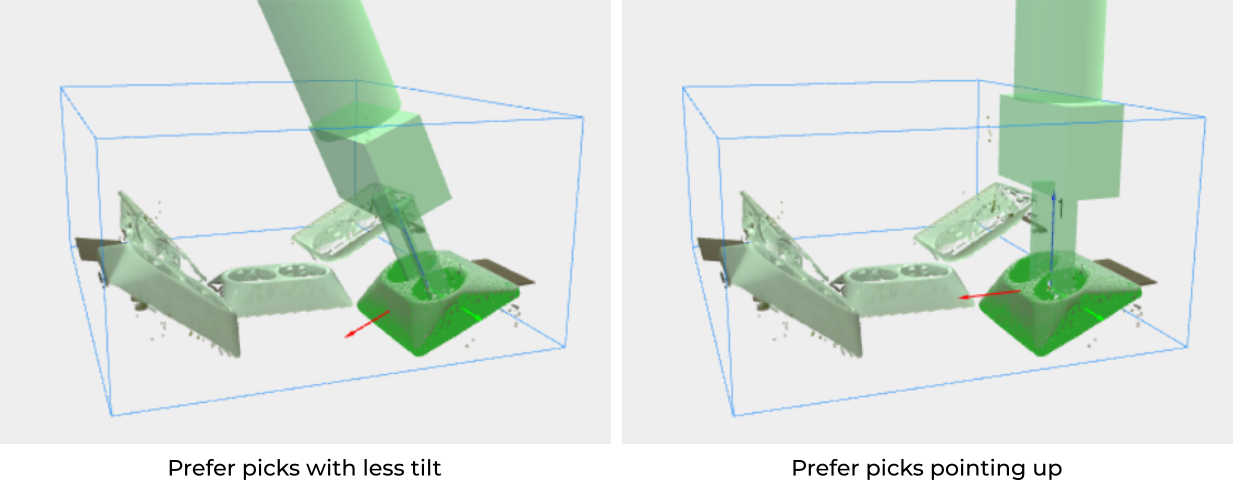
Tool Z rotation
Rotation about the tilted Z-axis helps to reduce robot motions, especially of the last wrist joints, which tend to be slower. It has three modalities, which represent equivalent ways (symmetries) in which the tool can pick a part:
Full-circle: The tool can pick the part equally well regardless of the rotation about Z. An example would be a single suction cup (below left).
180° flips: The tool can pick the part equally well from two discrete configurations that are 180° apart in Z. An example would be a rectangular magnet or a two-finger gripper (below center).
No rotation: The tool does not tolerate any rotational flexibility about Z. An example would be an asymmetric tool (below right).
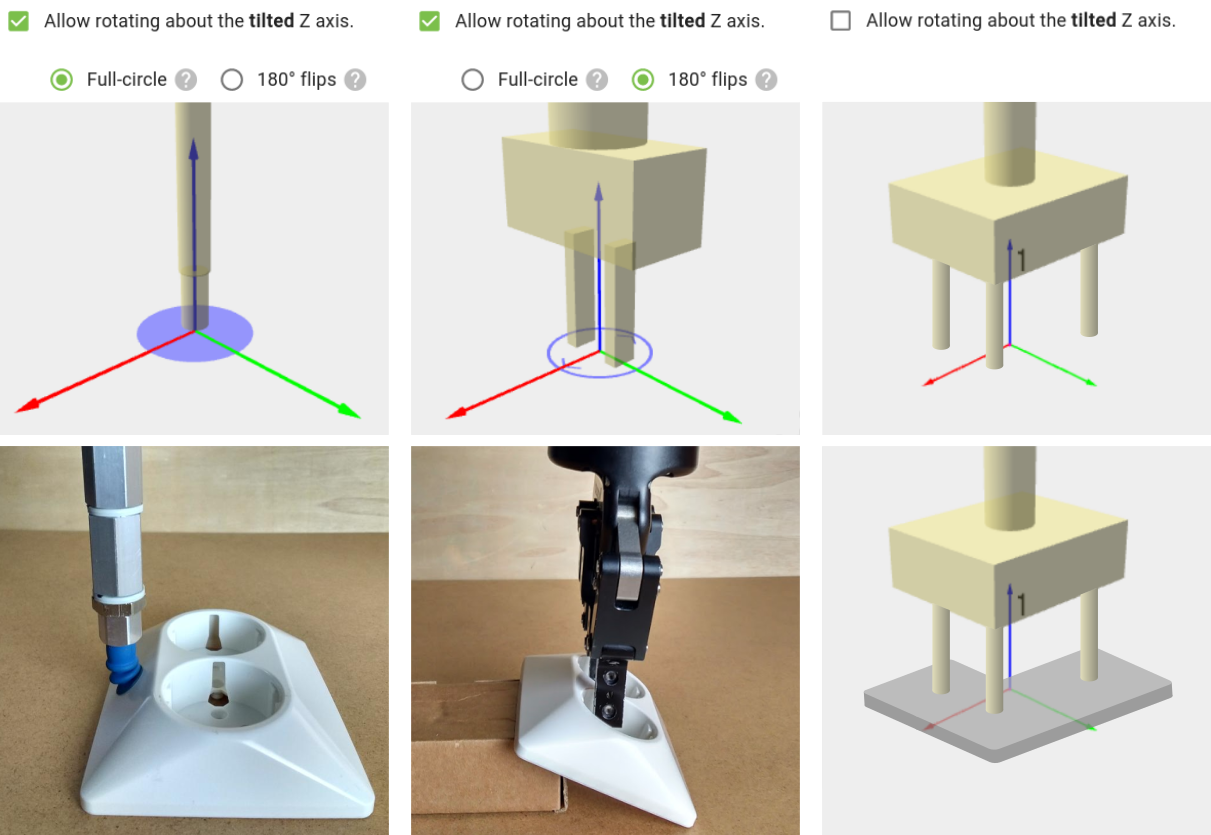
Passive hinge
A tool with a passive hinge is well suited for picking tilted objects from deep bins, while tilting the robot flange as little as possible. Minimizing robot flange tilt is associated with the advantages mentioned here.
The passive hinge also increases the likelihood of successfully extracting a grasped part from the bin. When a part to pick is partially blocked or constrained by surrounding bin parts, the passive hinge motion allows the grasped part to move around them during bin extraction in a way that the grasp is more likely to be maintained.
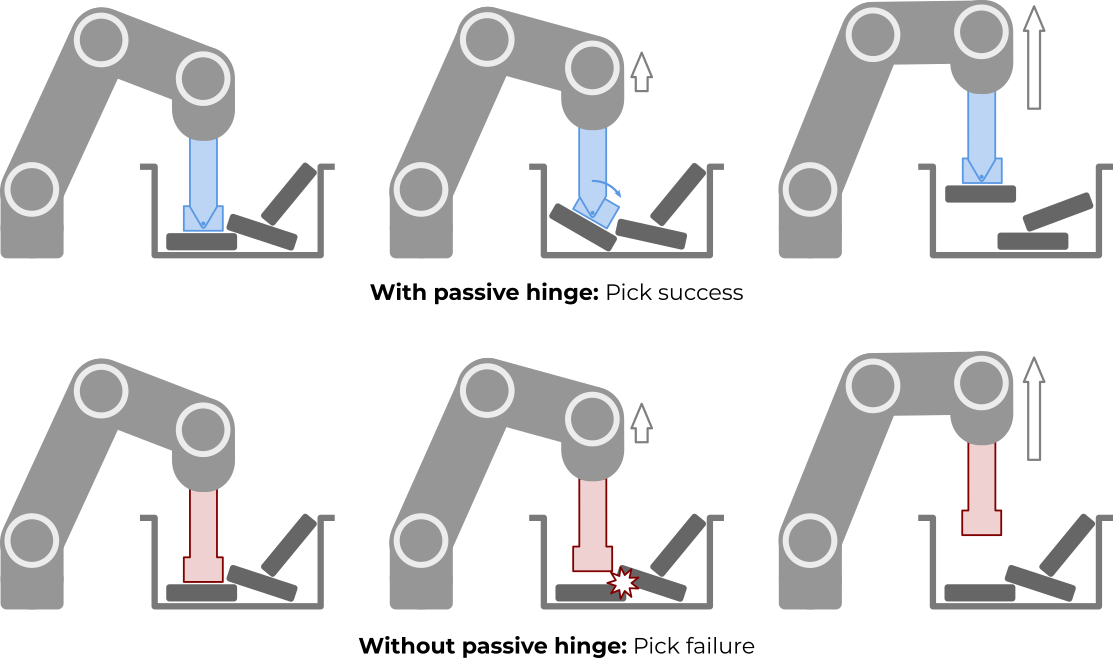
Note
Pickit offers gripper solutions with a passive hinge that seamlessly integrates into the product.
The billet picker gripper (patent pending) is shown below, and can also be previewed by exploring the example snapshots in the examples/billets
folder.
Software support for the billet picker is provided by the Pickit smart gripper license module. To learn more, contact sales@pickit3d.com.
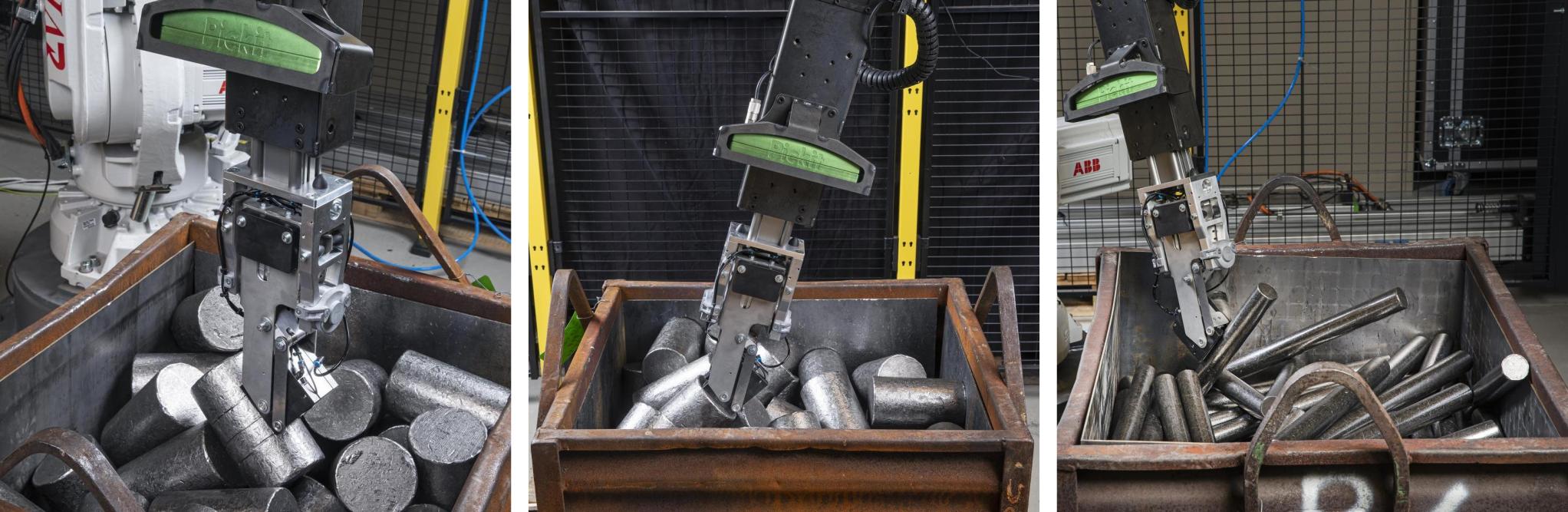