Should the camera be fixed or robot-mounted?
The Pickit cameras allow two mounting options: Robot-mounted or fixed to a rigid structure. In this article, you will find guidelines that help you to decide which camera mount is best suited for your application.
Broadly speaking, a robot-mounted camera is the most flexible option, and can produce more consistent part detection performance. On the other hand, fixed cameras are easier to set up and are typically well suited for simpler and smaller applications.
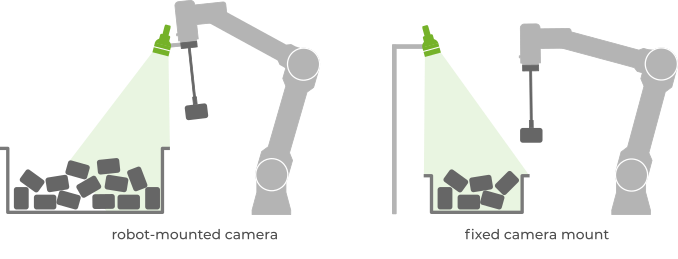
When to use a robot-mounted camera?
Pickit cameras are compact and lightweight, which allows them to operate mounted on a robot. A robot-mounted camera is very flexible, allowing to perform detections from multiple detection points, that is, multiple camera viewpoints. This enables a single camera and robot pair to operate on large detection regions (deep bins, high pallets), to pick from multiple stations, and can also produce more consistent part detection performance.
This section describes the different advantages in detail, as well as the compromises that need to be considered.
Large detection regions
The most typical situations where the detection region is larger than the camera field of view are:
High pallets or deep bins. Parts can span a height that exceeds the recommended camera depth range. When they do, move the detection pose down as the height of the parts decreases.
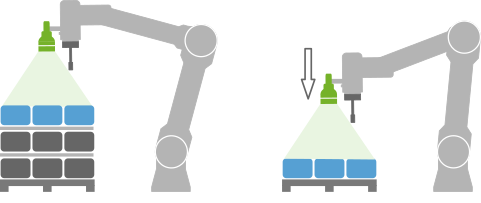
Wide bins or pallets. Bins and pallets can be wider than the field of view at the recommended camera depth range. When they do, attach the ROI to the robot base, and cover the surface with multiple overlapping detection poses (example).

The overlap between the different detection poses should at least be as large as the longest dimension of the part to detect. This condition applies to the camera depth range where parts are expected to be visible, such as all the way up to the bin top in the below example.
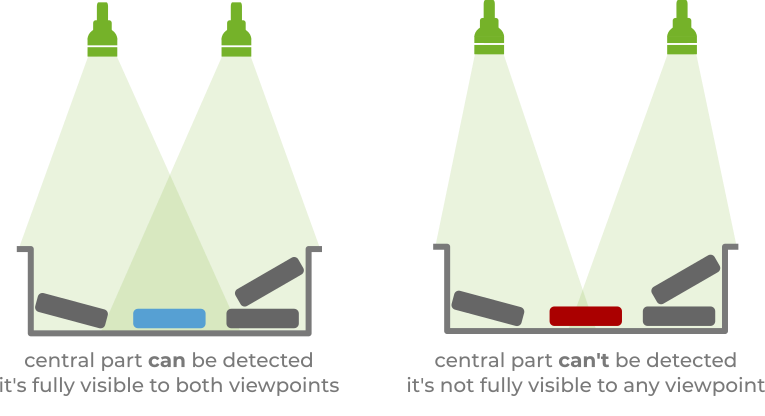
Better detection quality
Moving the detection pose down on high pallets or deep bins (as mentioned above) not only keeps the parts to pick within the field of view, but also preserves a similar distance to the camera as the bin or pallet empties, which results in more consistent detection quality.
Additionally, the distance between camera and parts can be made shorter than with a fixed camera mount, which results in higher detection quality (accuracy is better at shorter distances).
Finally, being able to run detections from different camera orientations can increase the likelihood of detecting more parts. This strategy can be particularly useful for detecting parts with reflective regions, that are occluded, or close to bin sides.
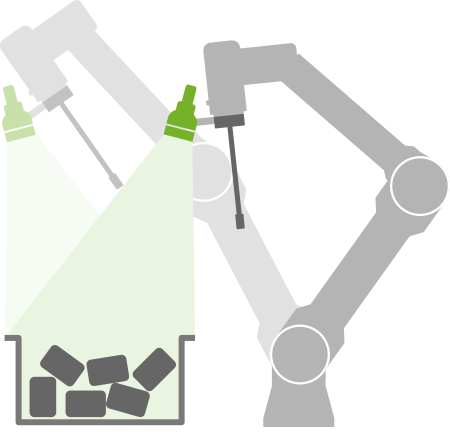
Multiple picking stations
In some applications, feeding new parts to pick is a process that can take a non-negligible amount of time, such as when an empty bin or pallet needs to be replaced. In the below example a robot can pick from two picking stations, such that once bin 1 is empty, it immediately switches to bin 2. Bin 1 is then replaced while picking takes place in bin 2.
Bin replacement can take as long as it takes the robot to empty a bin without affecting part throughput. Multiple picking stations are especially useful in applications where this duration can be long or even variable, such as when a forklift needs to be available to drive in and swap bins.
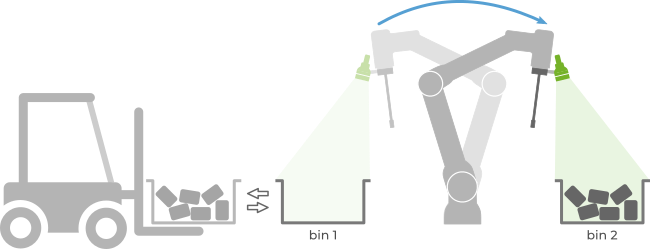
Another usecase for multiple picking stations is kitting applications, where a robot puts together a kit (below right) by combining different items from different pick stations (bins 1 and 2 below left).
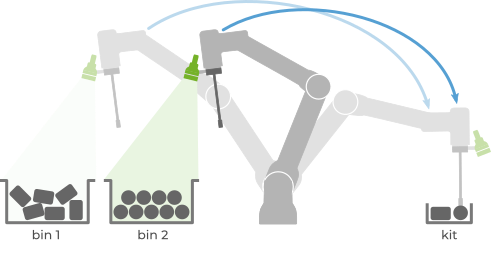
Compromises
The average pick and place cycle time is often slightly longer for robot-mounted cameras than for fixed cameras. A typical cycle time optimization consists of performing robot motions in parallel to object detection.
Object detection consists of two steps, image capture (typically shorter) and image processing (typically longer). Fixed camera mounts can mask both image capture and processing times, whereas robot-mounted cameras cannot mask image capture time, as the robot must remain stationary during this step. When applicable, one way to reduce this overhead to a fraction is to pick multiple parts per detection.
Converning the hardware setup of a robot-mounted camera, the main aspects to consider are:
The camera should be rigidly mounted to the robot, and well-protected against unexpected collisions in all directions.
Note
If using a low-payload robot, make sure that the weight added by the camera and its protection is acceptable for the application.
Its location should be optimized for good image captures, yet should also allow for a slender robot tool design.
Its location should also not hinder the robot workspace. That is, the camera should not collide with the robot, especially when performing tilted wrist motions.
When connecting the camera, follow the best practices on how to route its cables.
When to use a fixed camera?
Single camera
A single camera with a fixed mount is recommended when:
The detection region is fully contained in the camera field of view, and the detection quality meets application requirements over the entire detection region. Typical examples are picking from small or shallow bins, or from a conveyor.
The camera location satisfying the above condition is such that the robot doesn’t collide with the camera or its mounting structure while performing a pick.
There is a single picking station, and feeding new parts to pick has a negligible impact on part throughput requirements.
When all of the the above conditions apply, a single fixed camera is a good choice for two main reasons. On the one hand, cycle times can be slightly faster, as both image capture and processing times can be masked with robot motions. On the other hand, the hardware setup can be simpler, as there’s no need to protect the camera, nor to route its cables through the robot. However, note that an adequate camera mounting structure might require some engineering effort to make it rigid, isolated from vibration sources, and out of the robot motions space.
Multiple cameras
Using multiple fixed cameras can sometimes be an alternative to a robot-mounted camera, as it strikes a good balance between application performance and a simple hardware setup. However, this configuration is applicable to a limited set of cases, where there are only a few (typically two) fixed viewpoints, such as the case shown below. It consists of an application that meets the criteria for using a single fixed camera that has been expanded to have two picking stations.
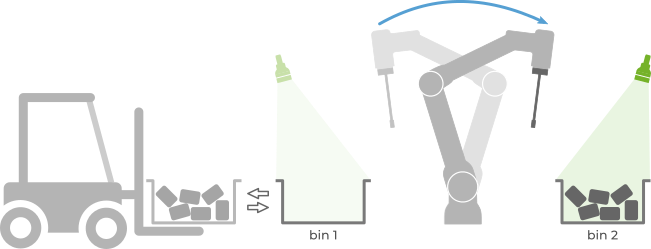
This option becomes impractical for economical and technical reasons once multiple detection points per picking station are required, such as when detection regions are large and require consistent detection quality throughout their volume.