Warning
You are reading the documentation for an older Pickit release (2.4). Documentation for the latest release (3.5) can be found here.
Software release 2.4
Pickit 2.4 focuses on improving the experience and performance for axisymmetric objects, like billets, pipes, shafts, rings and camshafts. Formally recognizing the symmetry of a shape opens the door to optimizations and picking possibilities, which are thoroughly leveraged by this release.
Teach cylinder model
The Teach engine has been upgraded to support cylinder models, which is ideal for detecting pure cylinders. Whereas before you had to teach a cylindrical part by placing it under the camera or uploading a CAD file, now you only need to specify a length and diameter. Choose how you intend to pick the cylinders, and Pickit takes care of the pick point definition for you. Furthermore, by letting Pickit exploit the cylindrical geometry, both detection speed and accuracy are optimized.
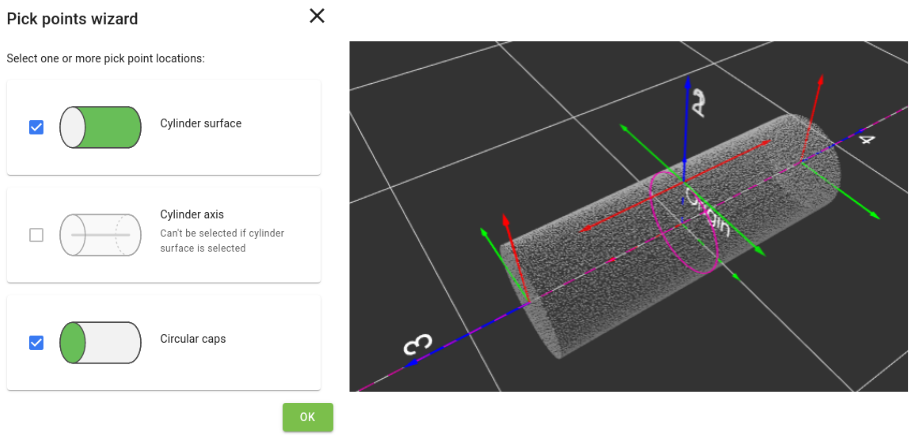
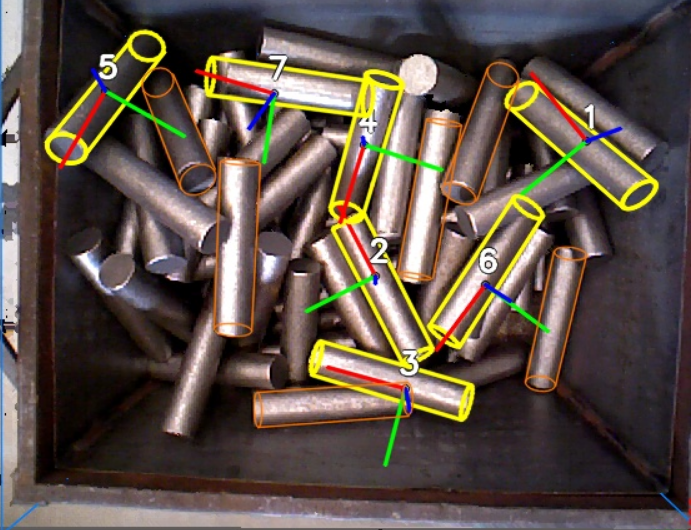
Are you constantly switching between different sized cylinders, but don’t want to open the web interface to teach a new model everytime? Now you can optionally set the cylinder dimensions directly from the robot program, speeding up the setup of different production settings.
Shape symmetry
If you want to pick a symmetric part like a pipe, a ring or a shaft, you can now specify its symmetry axis and make pick points aware of it. Pickit exploits the motion freedom introduced by this symmetry to increase the likelihood of the part being pickable.
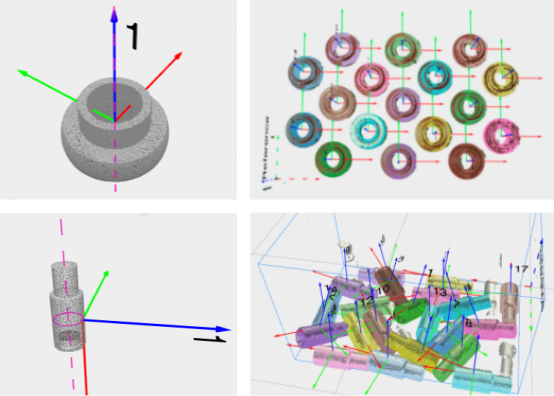
Flexible tools instead of flexible pick points
In Pickit 2.2, we introduced the concept of flexible pick orientation, which allows pick points to tolerate some orientation variability without compromising pick success. This can, in fact, increase the likelihood that a part is pickable.
In order to better model different types of grippers, we moved the specification of this flexibility from the pick point to the robot tool definition. Don’t worry! Your existing product files will be automatically converted to this new specification.
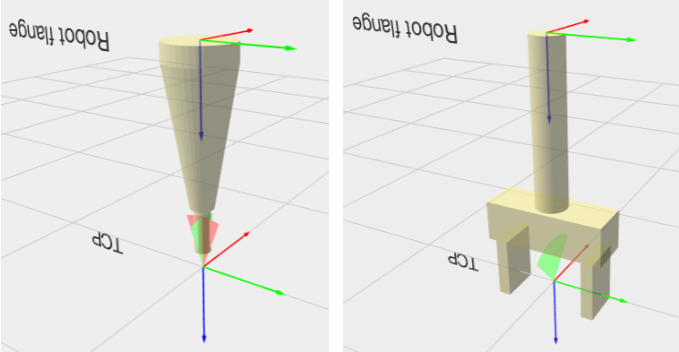
Minimum distance between robot flange and bin
It is sometimes desired that the robot flange, when picking objects, does not deviate too much laterally above the ROI or bin. This is particularly relevant when there are collision obstacles close to the bin like poles, fences or other tall structures, as shown below. It is now possible to limit how much the robot flange is allowed to deviate away from the bin walls.
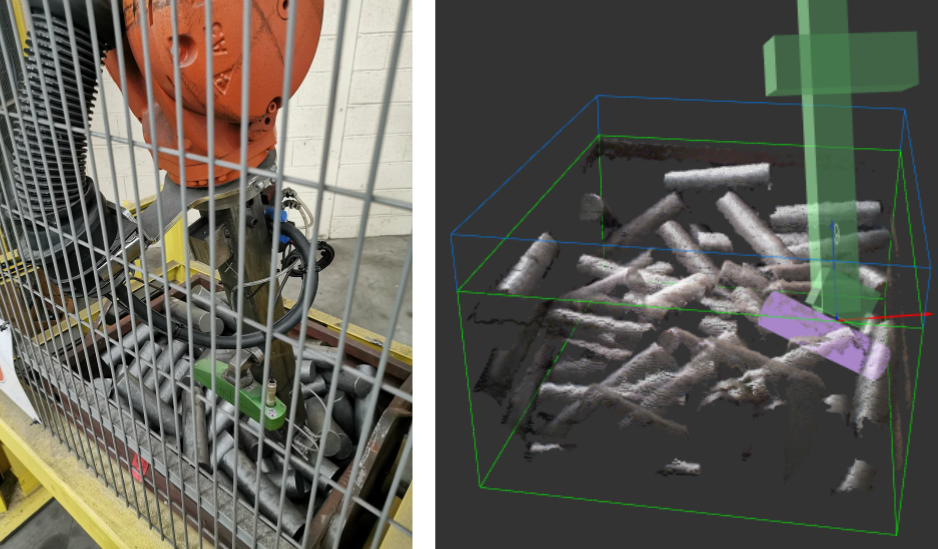
Temporarily avoid unpicked objects
The success of many feeding applications relies on a steady flow of picked objects, which in practice can be hindered by various reasons. A typical example is when the gripper is not strong enough to establish a firm pick on an object that is locked in place by neighboring parts. In these situations, it is important to temporarily avoid unpicked objects, and prevent the robot from repeatedly going to the same hard-to-pick object, and potentially get stuck in an endless loop.
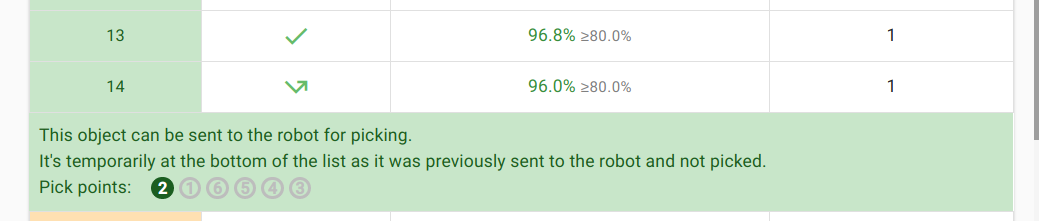
Picking experience in Flex
Pickit Flex now benefits from all the picking improvements that have been added to Pickit Teach since version 2.2, like flexible pick orientation, symmetry axes, and the different pick strategy options.
If you are picking basic shaped-objects with mixed dimensions, Pickit will find more pickable parts with potentially less robot motions.
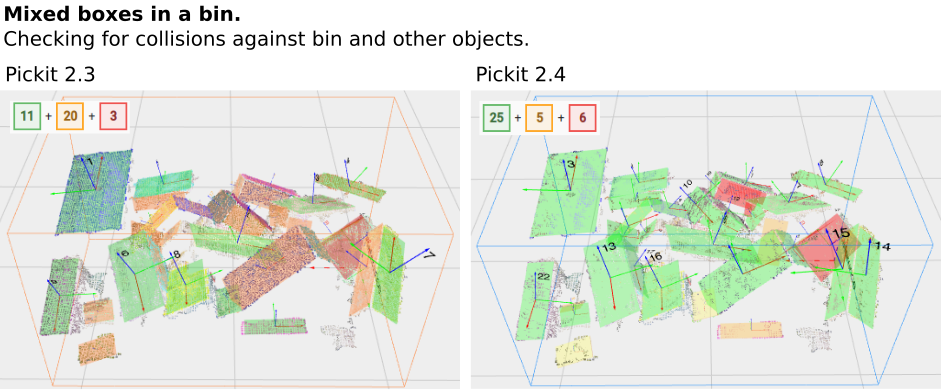
Get the update now
If you have an older Pickit version and would like to try 2.4, check out how you can upgrade your system.